Is Job Loss Due to Automation a Reality in the Fabrication Sector?
July 16, 2019
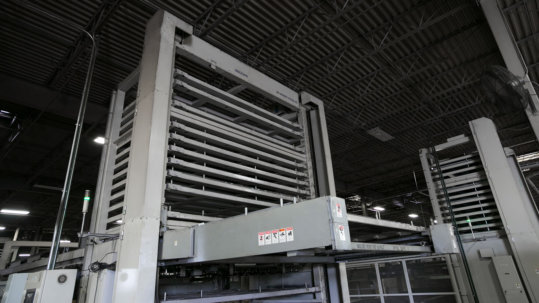
Is automation leading to job loss across the U.S. manufacturing sector? Theories have varied widely over the past few years and the debate is likely to continue for some time. In our experience, however, automation is not replacing workers, but allowing the same level of production to take place in the face of a diminishing manufacturing talent pool. At the same time, the necessity for technically competent workers possessing skills in the trades is at an all time high.
The Effect of the Skills Gap
According to a 2018 study from Deloitte, the skills gap may leave an estimated 2.4 million positions unfilled between 2018 and 2028. The majority of manufacturing companies have skilled positions open at this moment with very few takers. In many cases, to maintain production levels and grow a business, they have been forced to find ways to get product out the door with fewer people. Automation allows companies to do that but only if they have the operators capable of running and troubleshooting the advanced machinery.
In addition, freeing technically talented individuals and introducing them to technology and automation can energize and motivate them. As Gregory Ferenstein stated in a recent Forbes article, “Technology is increasing the number of high-skill jobs and better utilizing latent creative abilities that otherwise were wasted before routine jobs were automated.”
We have certainly found this to be the case. That’s the reason people in our organization tend to learn and move up rather than get frustrated and leave.
A Practical Example
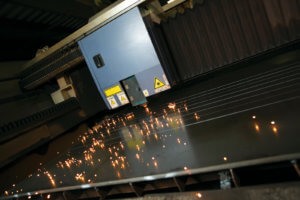
Our Mitsubishi laser cutting machines are tied into an FMS (flexible manufacturing system), where 22-shelf towers store raw materials in
various thicknesses, and an automated loader tends to the machine. This completely removes the need for the operator to go and find the raw
material for the next setup and then manually load the laser cutting machines. As plates are laser cut, the unload process is automated as well.
This kind of automation frees up operators to tend to more skilled jobs that they are better suited for, or can learn to do. The software that runs
the system allows scheduling of production runs which means the workflow is efficient. Not only that, since the system is tracking all of the
work being done in the FMS, the data is there for us to analyze utilization times for each machine.
Is Automation Enough?
Not on its own. We still need all the skilled workers we can find to coordinate with the automation. That’s why we have very robust recruiting programs in place to keep up with our current needs. (See Fabrication: The Pathway To A Bright New Future).Besides, even in these modern times, there are circumstances when nothing can compete with talent and hard-won human experience.
Why No New Workers?
As reported in U.S. News and World Report, “less than one in 10 employers say that higher education institutions are adequately preparing tomorrow’s workers, while a majority of educators think they are, in fact, sufficiently equipping future employees.”
The article quotes experts who agree that “The remedy to that mismatch begins with collaboration between educational institutions and the private sector.”
That is why we chose to become an active participant in the Workforce Ecosystem of Lake County which is comprised of the College of Lake County, Lake County Tech Campus, Workforce Development and Lake County Partners (See Building a Solid Manufacturing Community).
In our opinion, a judicious use of automation, in conjunction with talented and skilled workers, is the key to the highest levels of production and quality.
Sources
- 2018 Skills Gap in Manufacturing Study. https://www2.deloitte.com/us/en/pages/manufacturing/articles/future-of-manufacturing-skills-gap-study.html
- The Future of Automated Job Loss May Be Brighter Than Ever. https://www.forbes.com/sites/gregoryferenstein/2018/04/19/the-future-of-automated-job-loss-may-be-brighter-than-ever/#594bab3f11ae
- How to Prepare for the Fourth Industrial Revolution. https://www.usnews.com/news/national-news/articles/2019-05-22/how-to-prepare-for-the-fourth-industrial-revolution